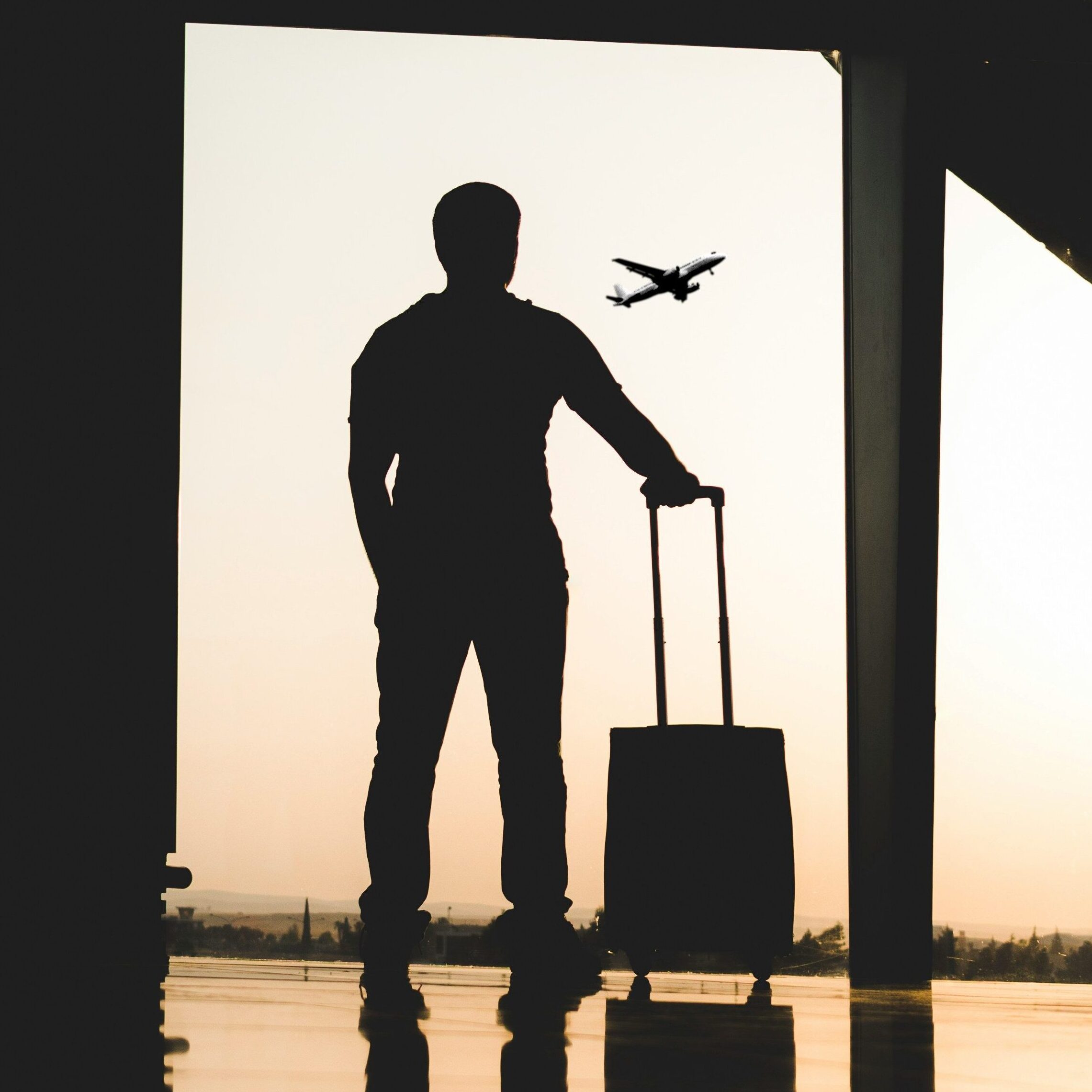
When an aircraft goes AOG — Aircraft on Ground — it means one thing: a critical part has failed, and the plane can’t take off until it’s replaced. For airlines, MROs (maintenance, repair, and overhaul providers), and operators, time is quite literally money. Every hour of downtime can cost $10,000 to $150,000+, depending on the aircraft and situation.
In these high-pressure moments, Onboard Couriers (OBCs) play a crucial role in aviation logistics. They provide the fastest possible method to get that one part — whether it’s an avionics module or a brake assembly — where it needs to be.
This article breaks down:
- What an OBC is and how it works
- Why OBC is ideal for AOG scenarios
- What parts can be shipped this way
- Real-world examples
- A step-by-step look at the process
🧳 What Is an Onboard Courier (OBC)/ Hand Carry?
An Onboard Courier is a trained logistics professional who personally accompanies time-critical cargo — typically as carry-on or checked baggage — aboard a commercial passenger flight. This approach bypasses the delays and limitations of traditional air cargo handling.
Instead of routing freight through warehouse hubs or waiting on scheduled air cargo flights, the OBC takes the part through airport security, flies on the earliest commercial flight, and hand-delivers it at the destination.
Think of it as point-to-point human express freight, built for speed and accountability.
🛫 Why OBC Is the Go-To for AOG Situations
When an aircraft is grounded, the priority is clear: get the part there as fast as humanly possible. Every delay not only impacts operations but risks missed connections, aircraft repositioning, compensation payouts, and cascading scheduling issues.
🚨 OBC Advantages for AOG:
- Speed: Booking the next available commercial flight (often within 1–2 hours)
- Security: A single person handles the part from pickup to delivery
- Customs Clearance: The courier walks the part through customs directly
- 24/7 Coverage: Global courier networks enable rapid dispatch across continents
- Flexibility: Couriers can switch flights or routes in real time to adapt to delays
For parts that are small enough to carry — avionics, flight computers, sensors, or tools — OBC is often faster than any cargo charter.
📦 What Kind of AOG Parts Can Be Shipped via OBC?
Because couriers must travel as passengers, OBC is typically used for items that:
- Fit in a carry-on (up to ~22″ x 14″ x 9″ / 55cm x 35cm x 22cm)
- Or fit in checked luggage (typically under 32 kg per bag)
✅ Common AOG parts shipped via OBC:
- Avionics control units
- Oxygen masks and safety components
- Hydraulic valves
- Flight sensors and transponders
- Wheels and brakes (compact units)
- Critical paperwork or certifications
⚠️ Hazardous materials, oversized cargo, and items requiring temperature control may need a dedicated air charter or specialized freight solution.
🧭 Real-World Example: AOG Response with OBC
Scenario:
An airline in São Paulo, Brazil has a grounded Airbus A320. The part needed — a flight computer — is only available in Madrid, Spain.
Without OBC:
Standard cargo would take 24–48 hours to arrive, with delays at export handling and customs.
With OBC:
A courier in Europe picks up the unit within 60 minutes, boards a commercial flight to GRU that evening, and hand-delivers the part at the airport the next morning. The aircraft is airborne again in under 18 hours.
That’s the difference between lost revenue and recovered schedule.
🔁 OBC Workflow: How It Actually Works
Here’s a breakdown of the typical OBC process during an AOG event:
- Request Received
A client shares shipment details: part type, dimensions, pickup location, and destination. - Nearest Courier Dispatched
The logistics team identifies the closest available certified OBC and confirms passport/visa validity. - Flight Options Reviewed & Booked
The fastest commercial itinerary is selected, balancing flight time and airport handling. - Cargo Collected & Secured
The courier retrieves the shipment and prepares it for travel (carry-on or checked). - Live Tracking Provided
Milestones are updated in real-time: pickup, check-in, in-flight, arrival, handover. - Delivery at Destination
Courier clears customs, exits the airport, and delivers directly to airline, hangar, or technician.
📌 Key Takeaways
- OBC is the fastest shipping method for small AOG parts, outperforming scheduled cargo and even charter in many scenarios.
- It’s ideal when delays could shut down operations or lead to significant loss.
- The service combines speed, personal handling, and customs efficiency, making it a critical tool in aviation logistics.
If you’re an airline, MRO, aerospace manufacturer, or logistics provider handling AOG shipments, it’s essential to have OBC in your toolkit — not just for convenience, but for cost avoidance and operational continuity.